In the dynamic climates of Dorset and Hampshire, industrial and commercial buildings face unique challenges that can compromise the integrity of their roofing systems. Regular maintenance is not just a recommendation, it’s a necessity. Ensuring the longevity and functionality of your roof protects your investment, maintains safety standards, and prevents costly disruptions to your operations.
Common Roofing Issues in Industrial Settings

Industrial roofs are exposed to various stressors that can lead to significant problems if not addressed promptly:
- Leaks and Water Damage: Often resulting from deteriorated sealants or punctures, leading to interior damage and mold growth.
- Ponding Water: Flat or low-slope roofs may accumulate water due to inadequate drainage, accelerating material degradation.
- Thermal Movement: Temperature fluctuations cause expansion and contraction, potentially leading to cracks and splits in roofing materials.
- Corrosion: Metal components are susceptible to rust, especially in coastal areas like Dorset and Hampshire.
- Blocked Gutters and Downpipes: Debris accumulation can impede water flow, causing overflow and potential structural damage.
Addressing these issues through regular maintenance can prevent minor problems from escalating into major repairs.
Benefits of Regular Roof Maintenance
Implementing a consistent maintenance schedule offers numerous advantages:
- Extended Roof Lifespan: Routine inspections and timely repairs can significantly prolong the life of your roofing system.
- Cost Savings: Preventative maintenance is more economical than extensive repairs or full replacements.
- Enhanced Safety: Regular checks ensure structural integrity, safeguarding employees and assets.
- Energy Efficiency: Well-maintained roofs provide better insulation, reducing heating and cooling costs.
- Compliance with Regulations: Adhering to maintenance schedules helps meet health and safety standards, avoiding potential fines.
By investing in regular maintenance, businesses can ensure operational continuity and protect their bottom line.
Before:
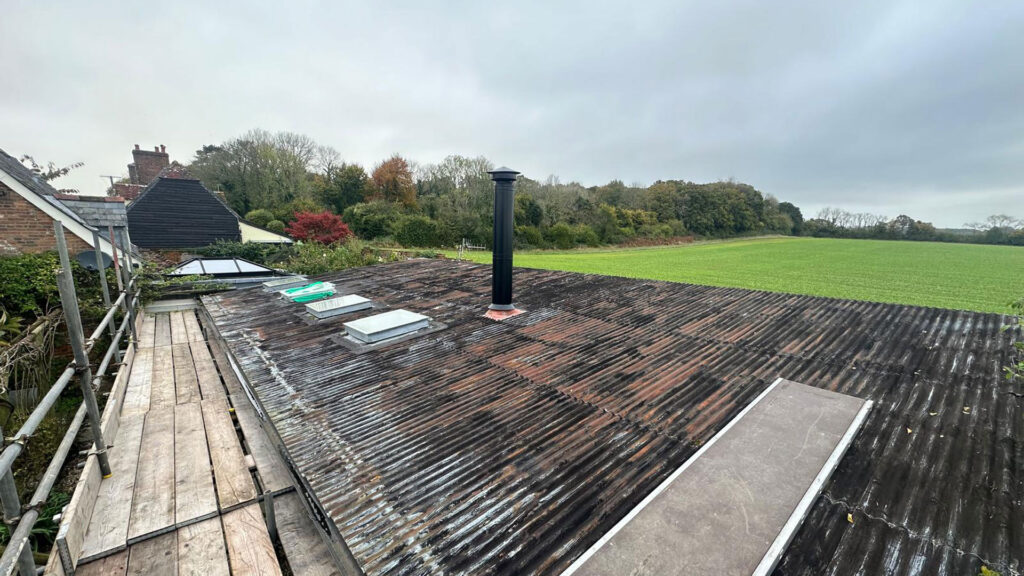
After:
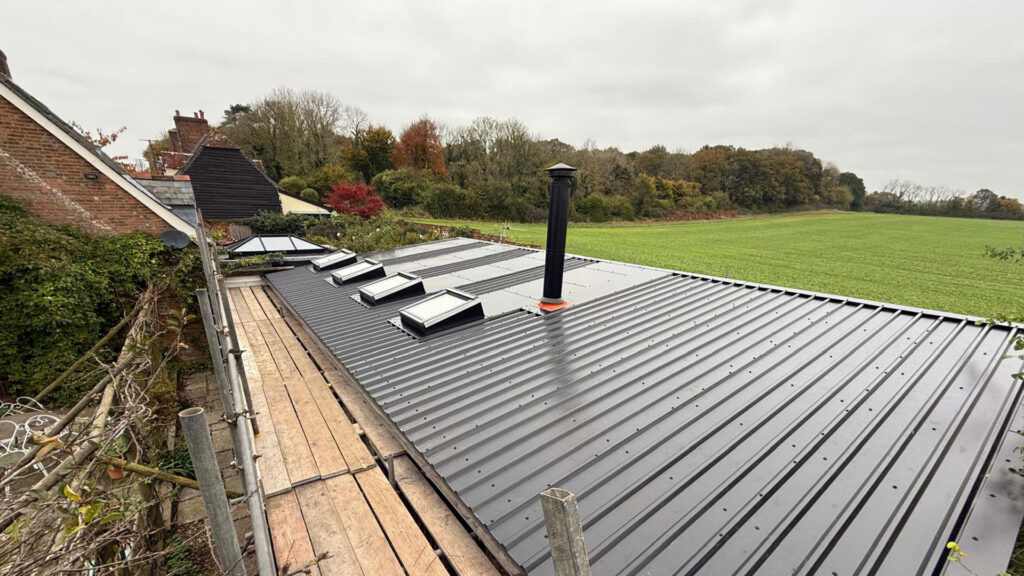
Tips for Scheduling Inspections
To maximise the effectiveness of your maintenance efforts, consider the following guidelines:
- Biannual Inspections: Conduct inspections in spring and autumn to prepare for seasonal weather changes.
- Post-Storm Assessments: After severe weather events, check for damage that may not be immediately apparent.
- Professional Evaluations: Engage certified roofing specialists familiar with industrial systems for thorough assessments.
- Detailed Record-Keeping: Maintain logs of inspections, repairs, and maintenance activities for reference and compliance purposes.
- Customised Maintenance Plans: Develop a schedule tailored to your specific roofing materials and environmental conditions.
Proactive planning and consistent monitoring are key to maintaining a robust roofing system.
For businesses in Dorset and Hampshire, ensuring the integrity of your industrial roofing is paramount. Don’t wait for minor issues to become major headaches. Schedule a comprehensive roof inspection today with our experienced team. Protect your investment and maintain uninterrupted operations by prioritising regular maintenance.
FAQs
Q: How often should industrial roofs be inspected?
A: It’s recommended to conduct inspections at least twice a year, typically in spring and autumn, and after significant weather events.
Q: What are the signs that my industrial roof needs maintenance?
A: Indicators include visible leaks, water stains, sagging areas, rusted components, and increased energy bills due to poor insulation.
Q: Can regular maintenance really extend the life of my roof?
A: Absolutely. Consistent maintenance can prevent minor issues from escalating, thereby extending the lifespan of your roofing system and saving on costly repairs.